How CalPortland streamlined environmental compliance with Mapistry
CalPortland, a leading building materials company, used Mapistry to modernize its compliance processes with automated data tracking and digitized inspections.
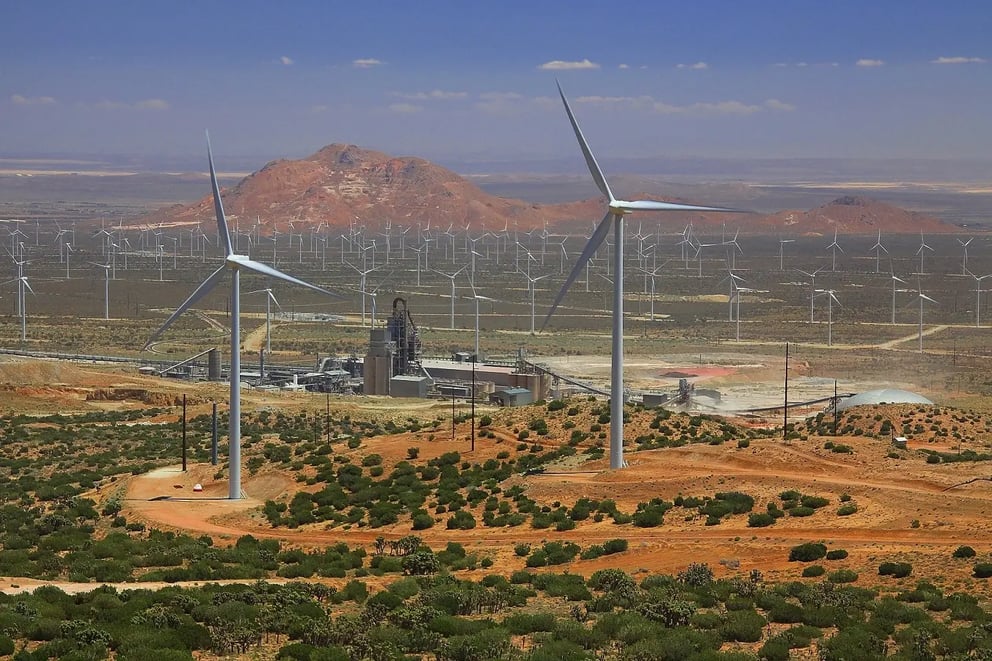
CalPortland, a leading building materials company, operates cement plants, concrete ready-mix batch plants, mining operations, and terminals.
Managing environmental compliance across multiple locations was becoming increasingly complex. Their reliance on paper forms and spreadsheets led to inefficiencies, compliance risks, and data silos.
With Mapistry, CalPortland modernized its compliance processes, transitioning to a centralized, digital platform that automated data tracking, improved inspection accuracy, and provided real-time visibility for the environmental team.
Challenge 1: A paper-first system meant zero visibility
CalPortland’s compliance management relied heavily on paper logs, Excel spreadsheets, and email reminders, making tracking and managing the 15,000+ inspections conducted annually across multiple sites difficult.
When COVID hit, the problem escalated. With no centralized system, paper records had to be mailed between locations, delaying compliance reporting and making real-time visibility impossible.
“We were already eager to go digital, but as the world halted and reports were mailed from site to site, any access to documents in real time was lost.”
– Desirea Haggard, Director of Environmental Affairs
New employees inherited broken compliance systems
As each site operated independently with inconsistent systems, new employees on the environmental team had to spend months reverse-engineering systems and hoping for the best.
"As a new manager entered into their role with CalPortland, the first task on their to-do list was to recreate a system and manually set 15,000+ task reminders." – Desirea Haggard, Director of Environmental Affairs.
Challenge 2: Manual data entry risked limit exceedances and fines
On top of paper-based records, manual data entry was creating compliance risks. Instead of logging emissions and production data in real-time, environmental managers updated spreadsheets manually—often at the end of the month.
This meant critical exceedances of permit limits could go unnoticed for weeks—until the environmental manager finally had time to update the spreadsheet.
“Usually the environmental manager would do this at the end of the month when they have time. But we're all busy. Maybe you've exceeded an emission or production limit by the time they update the spreadsheet.”
– Kacy Vance, Environmental Manager
Waiting any longer increased the risk of regulatory action
The longer CalPortland maintained the status quo, the greater the risk of facing compliance challenges, as keeping up-to-date records related to inspections, corrective actions, and limits became increasingly difficult without a robust, real-time tracking solution.
Why CalPortland chose Mapistry
CalPortland evaluated multiple software providers but ended up choosing Mapistry. There were three aspects that gave Mapistry the upper hand:
- Centralized compliance: All environmental data — inspections, tasks, emissions, and production data — would be accessible in one place.
- User-friendly app for operations: Without operations using the tool and entering data, the project would fail. Mapistry’s intuitive app was easy to use on a phone or tablet.
- Customization: The ability to tailor inspections and reports to site-specific needs.
"It’s been kind of magical. All inspections, logs, tasks, documentation…everything shows up in one place." – Kacy Vance, Environmental Manager.
The transformation: An efficient and reliable compliance system
What used to take a day now takes an hour
Implementing Mapistry transformed environmental compliance for CalPortland. Instead of digging through paper binders, the team could now get complete visibility in one place.
“Twice now, we’ve had inspections where regulators requested records. They saw Mapistry, all the completed forms, and the review was so quick. What normally takes a full day of going through paperwork only took about an hour.”
– Desirea Haggard, Director of Environmental Affairs
Real-time data collection and no more exceedances
Instead of manually entering data into spreadsheets, each site was now logging data directly to Mapistry. This allowed anyone with access to the site to see how close they're getting to their rolling production limit — in real-time.
Kacy highlighted the ease of use for field teams: "The guys picked it up right away as far as entering their data goes."
15,000 inspections, mountains of paperwork, and no real-time data, sound familiar?
CalPortland’s environmental compliance was a chaotic system of paper logs, spreadsheets, and scattered reminders. When they switched to Mapistry, everything changed. Now, inspections, emissions data, and production tracking are all in one place, cutting down admin work and catching issues before they become violations.
If compliance feels like a full-time job, let’s make it easier.
Schedule a call with our team to learn more.