MMC Materials Achieves Results with Data-Driven EHS
Concrete leader shifts from paper to digital, boosts cross-team accountability and compliance
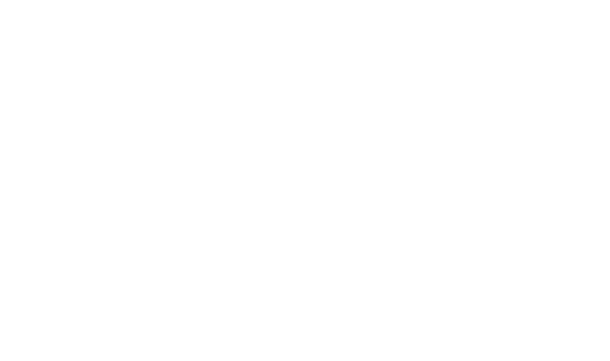
Business Needs
Quick and easy access to inspections forms and reports
Each of MMC Materials’ 80 concrete facilities executes 22 independent inspections daily complying with internal, local, state, and federal requirements. This amassed to over 12,000 inspections reports weekly accumulated on-site managers’ desks for review. With daily inspections tracked on paper, managers were permanently fixed in a sluggish backlog of tracing inspections and corrections.
To complete company-wide assessments, key stakeholders were required to travel from site to site and review paper reports in person. This was time-consuming and often, it was impossible to confirm if the inspections were completed timely or correctly due to inconsistencies in the forms.
Real-time assessment of accountability
The lack of standardization and mass effort required to track inspections and corrective actions impaired site managers’ ability to focus on other areas of plant improvement. The process was de-motivating and plant operators resorted to pencil-whipping to turn over inspection reports last minute rather than dutifully fulfilling daily compliance requirements.
Additionally, corporate staff had no way of verifying the quality of inspections being completed at their facilities without requiring them to hunt down the paperwork or rely on numerous calls and emails.
“We are really highly safety oriented so we have a lot of internal safety documents for safety inspections that we do on paper. These forms are required with the environmental forms every month or every quarter. However, they were not being done appropriately. To ensure they were done correctly, I’d go around in-person and do facility inspections and review my inspections with the facility manager, he may or may not remember everything I said.” Sonya Price – Area Safety Manager, GTR/Delta Areas
Tangible credibility of inspections and corrections
Forms consisted of a standard yes/no format for daily checks on equipment. The lack of accountability coupled with the ability to pencil whip what appeared to be positive inspection rates created a gap in their ability to improve safety and environmental operations.
There was no place in their inspections system to provide validation of their workflow and prove when issues were found and how they were addressed or by whom. Not only was it increasingly difficult to track progress but managers also lacked a way to review employee performance related to inspections duties.
Overcoming outdated state legislation
One hurdle MMC Materials faced in overcoming obstacles related to exclusively keeping track of inspections on paper was reworking Mississippi law. The MC Department of Environmental Quality did not accept electronic information site inspections. Following the pandemic, MMC Materials and other entities moved the state toward legislation to accept digital inspections forms in 2021 creating a segway for their implementation of Mapistry solutions.
MMC Materials is the largest ready-mix concrete producer in Mississippi operating 80 concrete facilities across Mississippi, Alabama, Florida, Tennessee, and Louisiana.
The company boasts nearly a century of experience in the concrete industry, serving its communities with honesty, excellence, and continuous improvement. Over the years, MMC Materials has been consistently recognized and gained respect for its commitment to safety and environmental excellence.
INDUSTRY
Building Materials
Ready-Mix Concrete
COMPANY SIZE
80 facilities
450+ employees
SOLUTIONS
Software Platform
- Analytics
- Mapping
- Tasks & Actions
- Inspections
- Inventory
Compliance Areas
- Stormwater
- Safety
- SPCC
- Air
- Facility
Resources
Case Study: PDF Download
Webinar: The EHS Journey from Paper to Digital
Spotlight: Area Safety Manager
Solution
Site dashboards for individual concrete plants
MMC Materials values honesty, excellence, and continuous improvement. With over 90 years of building their reputation on quality service, partnering with Mapistry solidified their commitment to putting safety at the forefront of operations.
Operating 80 concrete plants across the region requires MMC Materials to stay abreast of compliance for various states and local regulations. By partnering with Mapistry, the MMC Materials was able to quickly rollout site-level environmental and safety dashboards to empower plant managers to centrally monitor all of their unique compliance obligations in one location — including stormwater, air, SPCC, safety, and other required maintenance checks.
Visual indicators on the plant dashboard keep teams aware of any upcoming inspections and tasks as well as any overdue action items. Managers can also assign tasks and track on-site progress and performance all in one central location. Built-in automated notifications and reminders are another way to ensure that critical compliance checks are never missed.
“The quality of the inspections has resulted in less down time because things are being repaired before they are a problem. The plants are cleaner because tasks are done when they are supposed to be done.” Sonya Price – Area Safety Manager, GTR/Delta Areas
Centralized reporting ensures accuracy and accountability
The cumbersome and menial process of checking redundant paper forms cut into plant managers’ daily tasks so they were frequently set on the backburner. This left some plants untidy and rushed to meet compliance requirements when inspectors made their rounds.
Since moving safety and environmental inspections operations to Mapistry’s software and mobile app, MMC Materials stakeholders have seen consistent improvement in the accuracy and timeliness of plant inspection completion. Not only are facility managers saving time by addressing inspections issues before there is a reason for serious corrections, but plants are cleaner and safer than ever before.
Areas of operation outside of MMC Materials facilities management are seeing benefits from Mapistry’s customized forms functions as well, such as accounting and inventory.
“I oversee all the inventory. Previously, they had a sheet of paper they faxed or emailed in. Some would come in on the 1st, some on the 3rd. I’d have to call some on the 4th and say, hey I needed that yesterday. With Mapistry, I can just pull off the information I need. It saves time and improves accuracy by verifying the validity of their inventory.” Gary Scott – Assistant Area Manager
Instant access to reliable, company-wide compliance analytics
The lack of timely access to inspection reports and the inability to compare performance from site to site created a huge gap in which some plant operators could avoid completing inspections forms entirely. Mapistry’s intuitive mobile and cloud-based app changed that by giving everyone a big picture view of company-wide, site, and individual EHS performance.
“Those guys, I mean, you kind of get content with those paper forms. They didn’t even read the questions. They just knew yes, yes, yes, yes, no; yes, yes, no, no. They’ve done it so many times. Working with Mapistry gives them more accountability. I think if they know what to expect, you can expect more out of them,” said Gary Scott, MMC Materials’ Assistant Area Manager.
Through Mapistry’s pre-built analytics dashboards, key stakeholders can now keep a pulse on the compliance performance across all of their facilities and individual team members. They have been able to use this data to benchmark performance, spot areas for improvement as well as to recognize facilities and individuals who are going above and beyond to ensure plants are safe and compliant.
Additionally, quick and easy access to data analytics and the automation of inspection reports and task management ensures facilities have more time to improve operations rather than checking boxes. This system encourages accountability and pride in plant performance and as a result, MMC Materials’ plant safety record has improved.
Complete digital validation of workflow
Relying on basic yes/no inspections forms prior to moving to digital EHS compliance management with Mapistry, meant MMC Materials had zero validation of completion for daily inspections. Plant operators could check yes when an issue was found and yes when a correction was made, but there was no way for key stakeholders to track whether corrections were done timely or accurately.
Through the Mapistry dashboard, plant employees can fully document their workflow through the quick and easy upload of images and documents. This helps facility managers trace actions taken to correct inspections issues and senior management has access to full reports from anywhere at any time.
“I can now assign a task with the photos, they have access to everything. They can put their notes in there. We can take that whole process and scan in documents, add photos, track the completion. When it’s done we can see the whole process. They don’t forget what needs to be done. It’s there in their weekly email. They get an email when a task is assigned to them and they can document their process.” Sonya Price – Area Safety Manager, GTR/Delta Areas
Mapistry’s convenient off-line access feature through the mobile app allows inspections forms and supporting documentation to be completed and uploaded when internet access is unreliable or unavailable. This feature has made it possible for MMC Material’s remote plants to stay on top of their inspections while in the field. Once connected to the internet network, daily tasks are seamlessly updated in the Mapistry dashboard.
“The offline access helps too because some of our plants are remote. They can still take their pictures and make their notes. And when they connect to Wi-Fi or the internet, it uploads everything. So you haven’t missed anything, and you don’t have to remember to go back and do your inspection later because you’ve done it and it just uploads. It’s really nice!” Sonya Price – Area Safety Manager, GTR/Delta Areas
After implementing Mapistry
The MMC Materials team can now trust their inspections are completed timely and accurately, holding all key players accountable to uphold their values to continue to improve their performance, safety, and environmental impacts.
Mapisty has helped motivate and give accountability for compliance across our facilities. Managers can now take ownership in their sites so we’ve seen a big improvement in their performance.
“With the level of customization with Mapistry, we can access data that drives our mission to improve and earn respect as the best ready mix producer in the market we serve. And we can exceed our goals to ensure our operations are consistently safe and environmentally compliant.”
Create more proactive and accountable teams
Learn why the world’s leading industrial companies trust Mapistry to streamline EHS compliance
